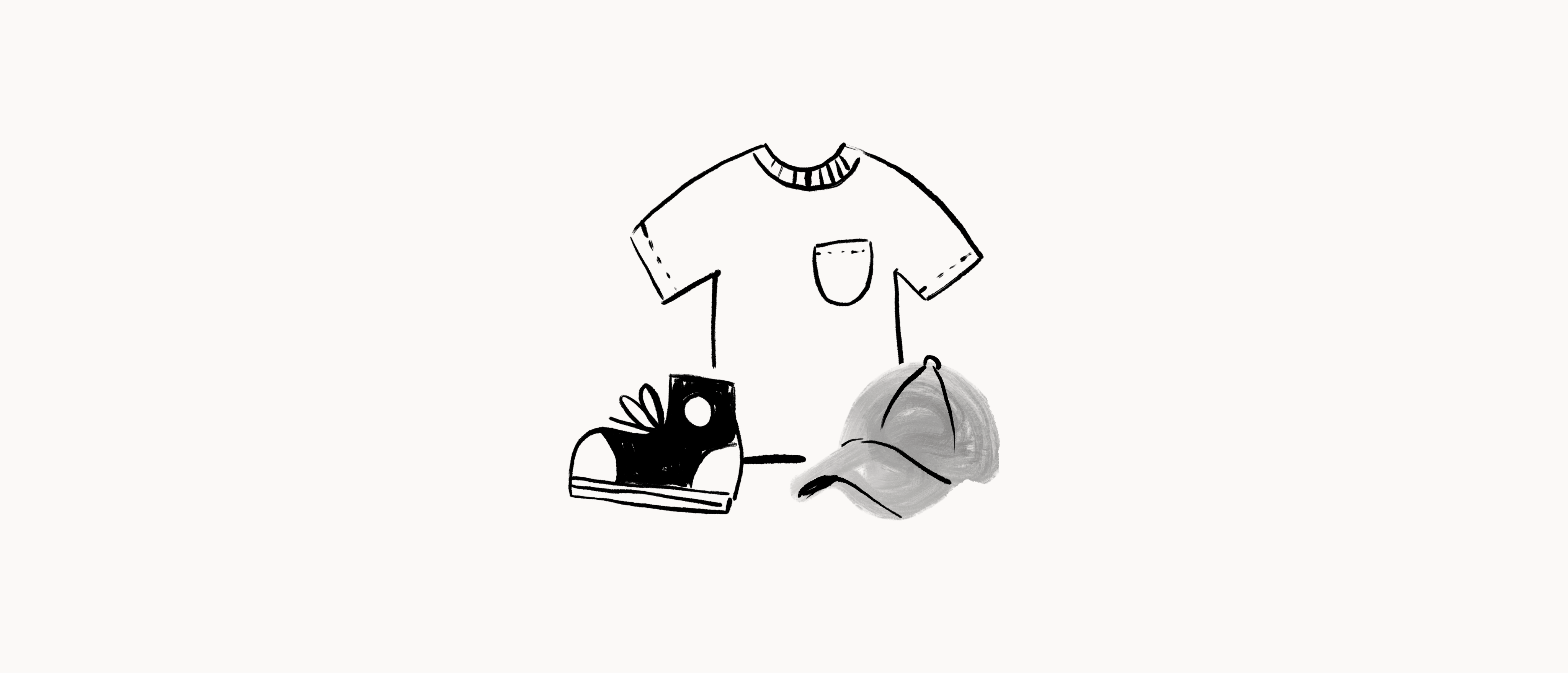
By Maja Carvell Strecker
7 minute read
Maja Carvell Strecker By Maja Carvell Strecker
7 minute read
When it comes to product longevity, quality isn’t a final checkpoint - it’s a mindset that has to be built in from day one. That’s the approach taken by Sika Footwear, a fourth-generation Danish company with over 150 years of experience producing occupational and safety footwear.
Faced with scattered, unsynchronized data across teams, Sika saw the need for a more structured approach to their quality control processes. “We had a lot of data, but it wasn’t synchronized,” says Morten Berthelsen, Sourcing Manager at Sika Footwear. “It was stored in all kinds of places - servers, inboxes, handwritten notes - which made it hard to work in a uniform way.”
To address these challenges, Sika turned to a tech stack that combined Delogue PLM and Qarma, a quality control platform designed to streamline inspections and compliance. The result? A more structured and data-driven workflow that bridges product development with quality control - ultimately supporting product longevity and regulatory compliance.
Connecting development and production
For Søren Riis Mønsted, Co-founder of Qarma, the integration between Delogue PLM and Qarma plays a critical role in connecting two worlds that often operate in silos. “Development and quality control can easily become disconnected,” says Søren. “If the teams don’t communicate, how can we know what’s being inspected actually reflects the original intent?”
By pulling product specifications directly from Delogue PLM into Qarma, quality inspections can be conducted with full visibility into the original design specs - everything from color and size to packaging details. It’s a simple, yet powerful integration that ensures nothing gets lost in translation between development and production.
Quality starts early
At Sika, the product development and quality control teams work closely to review and approve product samples early in the process. All relevant data is stored in Delogue - from certification documentation to custom fields that later inform inspections in Qarma. This early-stage alignment means fewer surprises later on.
As Søren puts it, “The earlier in the process you catch a defect, the cheaper it is to correct. If you can catch it before production starts, you save time, money, and reduce waste.”
“We cannot run it on thoughts and assumptions and feelings. Data never lie.”
Morten Berthelsen, Sourcing Manager, SIKA Footwear
Empowering inspectors and suppliers
Beyond internal alignment, the tools are also helping Sika empower their inspectors and suppliers. With Qarma’s mobile app, inspectors no longer need to juggle handwritten notes and outdated spreadsheets. Everything is uploaded and synchronized in real-time - photos, comments, and corrective actions.
“Now inspectors can focus on what they’re there to do - perform quality control - not on gathering files or formatting reports,” says Morten.
“The earlier in the process you catch a defect, the cheaper it is to correct.”
Søren Riis Mønsted, Co-founder, Qarma
The same goes for supplier collaboration. A structured, intuitive platform means suppliers have better visibility into what’s expected - and how to improve. “You can’t just tell them to ‘make better quality,’” Søren explains. “You need data to back it up. That’s how you create meaningful conversations and drive long-term improvement.”
A foundation for compliance and longevity
With increasing pressure from EU regulations on transparency, compliance, and sustainability, this level of structure is becoming non-negotiable. For Sika, it’s also a competitive advantage.
“Having everything documented and accessible helps us report, audit, and take action faster,” says Morten. “It’s an ongoing learning process - but it’s one that puts us in control.”
For any brand aiming to improve product longevity, the advice from both Sika and Qarma is clear: start early, stay structured, and make data your strongest tool.
Watch our webinar with the Qarma.
Morten Berthelsen from Sika Footwear, Jacob Nedergaard, Co-founder at Qarma and ESG Expert and Head of Communications at Delogue, Anja Padget, came together the 26th of March at 11 am to discuss how to embed quality into your product development process and ensure long-term success.