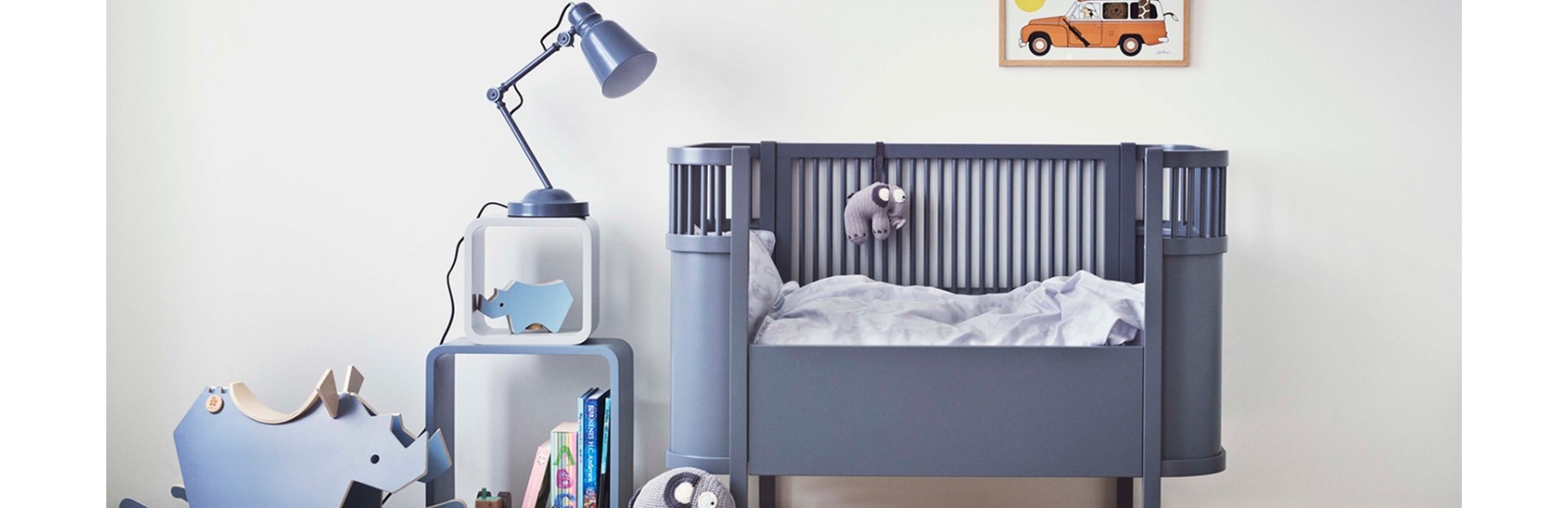
Sebra is a children’s interior design brand founded by Mia Dela in 2004. Sebra’s designs are a combination of unique and handcrafted products made from authentic materials, such as wood, wool, and organic cotton. They include furniture, lighting, textiles, tableware, and toys. Passion, respect, innovation, and diversity are all important elements in they way Sebra operated.
Improving efficiency and saving valuable time has always been an important goal for Sebra. It is the reason they implemented Delogue; to boost operational savings and traceability and work towards more efficient practices.
The potential of easily accessible data
Sebra was affected by the so-called full-inbox syndrome. They struggled to keep track and find updated information in times of vacation or illness and particularly when onboarding new employees. As they began to clean up the product data library, Sebra quickly realized the value of a dedicated solution to efficiently manage knowledge and streamline employees in design and production processes.
Improved operational savings through a single source of truth
Delogue PLM helps Sebra to keep track of relevant data and provides a single source of truth, eliminating the time they spent searching through Excel sheets and email inboxes. Mia Dela, Creative Director at Sebra explains:
“We investigated and searched for a product development tool that could be integrated with our Navision setup, and I can say for sure that Delogue PLM is the best solution for us.”
After the implementation of Delogue PLM, Sebra has experienced a more efficient and less time-consuming development process due to fewer errors and misunderstandings.
“Finding product information quickly and communicating with suppliers at every step of the process also makes it possible for us to promote transparency, and be more responsible as a company.”